Surface Options
Both systems in the market today offer a Heavy-Duty Cleat and a Tread Plate (Pooched) surface. MMARS offers a Diamond Plate surface as well, but it is rarely used.
The Heavy-Duty Cleats have an advantage over the other two surface options in that the spacing between the cleats allows rain, snow and debris to fall out between the cleats. The other 2 surface options do not do this and in adverse weather conditions the ramps can become slick.
The Tread Plate (Pooched) and Diamond Plate surfaces are approximately 30% more expensive than the 1/2” serrated Heavy-Duty cleat. The 30% applies only to the ramp surface cost.
A Tread Plate (Pooched) surface is required in loading containers with caster wheels or dollies with smaller wheels.
Our competition sells their system for loading helicopters using a Pooched Plate surface. They try and make the arguments that the spacing between the Heavy-Duty cleats creates a “bumpy ride” for a helicopter tail wheel and that the airmen can get a foot stuck between the cleats. We do not put weight into either argument. At JBLM the ramps had a 4” gap between each 2” wide cleat. The AH64 tail wheel easily ran up the center of the ramps (timestamp 4:25) and no toes were caught.
Though we do not believe it is necessary, we now put additional Heavy-Duty cleats on the middle ramps (for the tail wheel) so the gap between the cleats is 2” rather than 4”.
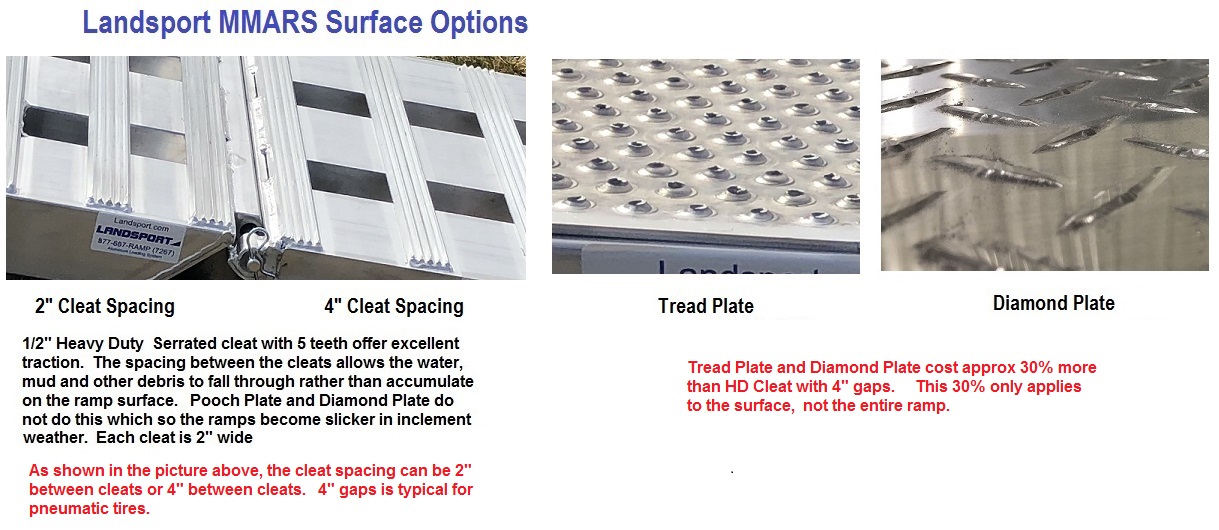
DISADVANTAGE OF TREAD PLATE (POOCHED) SURFACE
Typically, a unit purchases an aluminum shoring system to load up a variety of equipment. The surface chosen must stand up to ALL of the equipment that will use the shoring system. Helicopters are on the light end of the spectrum. Due to their relatively light weight, a Tread Plate (Pooched) surface can be used. When loading heavier equipment, however, the main tubes of the ramp will deflect as they are meant to. Since the Tread Plate (Pooched) surface is welded to the top of the ramps as an entire sheet it does not deflect. The result is that as the tubes deflect downward a high degree of stress is put on the welds that hold the sheet in place. Overtime, this may cause the welds to break. This does not occur when using Heavy Duty Cleat because each cleat is welded individually to the main tubes.
Here are 2 videos.
The video on the left shows that as the tubes deflect, the Pooch Surface actually lifts away putting more stress on the welds.
The video on the right shows that because each cleat is welded on separately, they deflect along with the tubes and the possibility of the welds breaking away is greatly reduced.
TREAD PLATE (POOCHED) SURFACE |
HEAVY-DUTY CLEAT |